Benefits of Laser Machine Welding for Metal Fabricators
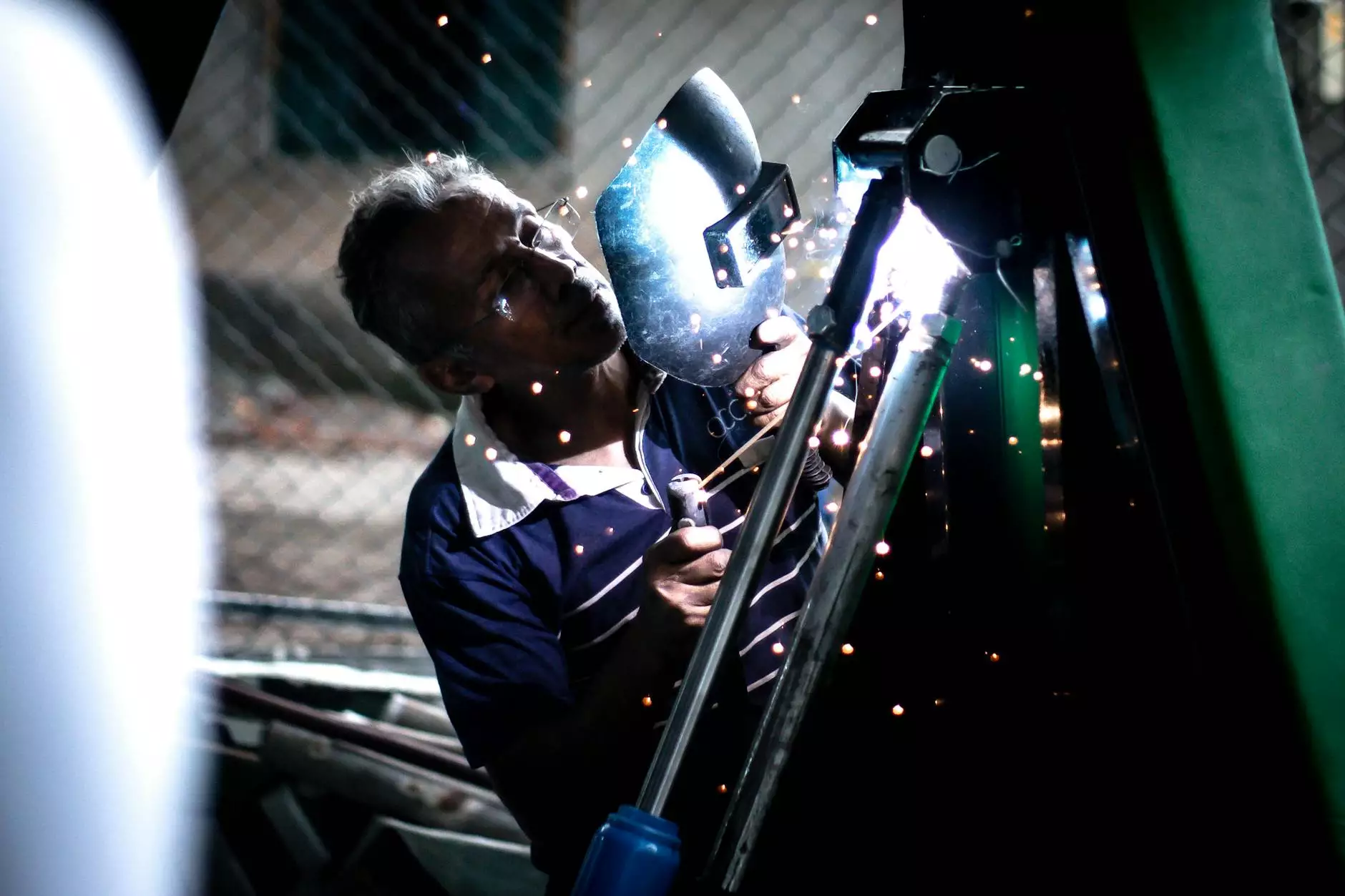
Introduction
When it comes to metal fabrication, precision and quality are essential. For businesses in the metal fabrication industry, keeping up with the latest technologies and techniques is crucial to stay ahead of the competition. One such technology that has revolutionized the industry is laser machine welding. At DPLaser.com, we offer cutting-edge laser machine welding services that provide numerous advantages for metal fabricators.
What is Laser Machine Welding?
Laser machine welding is a technique that utilizes a high-powered laser beam to join metal components together. Unlike traditional welding methods, laser machine welding offers precise control and accuracy, resulting in high-quality welds with minimal heat-affected zones.
The Advantages of Laser Machine Welding
1. Superior Precision and Quality
One of the main advantages of laser machine welding is its exceptional precision. The focused laser beam allows for accurate control, minimizing the risk of welding defects and ensuring consistent high-quality welds. This precision is especially beneficial for metal fabricators working on intricate or delicate projects.
2. Reduced Heat-Affected Zones
Compared to conventional welding methods, laser machine welding generates minimal heat, resulting in significantly reduced heat-affected zones. This not only improves the overall quality of the weld but also minimizes undesirable distortions and material damage, ultimately saving time and cost for metal fabricators.
3. Versatile Application
Laser machine welding can be applied to a wide range of metals, including steel, aluminum, and copper. This versatility makes it an ideal choice for metal fabricators working with different materials and allows for seamless integration into existing fabrication processes.
4. Increased Efficiency and Productivity
The speed and efficiency of laser machine welding are unparalleled. The precise control and high welding speeds enable metal fabricators to complete projects in a fraction of the time required by traditional welding methods. The increased productivity translates into reduced lead times and improved customer satisfaction.
5. Cost-Effective Solution
While laser machine welding may require an initial investment, its long-term benefits outweigh the costs. The reduced need for secondary operations, such as grinding or polishing, significantly decreases labor and material expenses. Additionally, the minimal heat input further reduces the need for post-weld treatments and lowers overall production costs.
6. Environmentally Friendly
Compared to conventional welding techniques that often involve harmful gases or chemicals, laser machine welding is a more environmentally friendly option. By utilizing a focused laser beam, it minimizes waste and reduces the impact on the environment, making it a sustainable choice for metal fabricators aiming to reduce their carbon footprint.
Conclusion
Laser machine welding offers metal fabricators unparalleled precision, quality, and efficiency. At DPLaser.com, we understand the needs of the industry and strive to provide cutting-edge laser welding solutions to help businesses excel. Take advantage of our state-of-the-art laser machine welding services to stay ahead in the competitive world of metal fabrication. Contact us today at DPLaser.com to learn more about how we can assist you and elevate your fabrication capabilities.