The Rise of Forged Carbon Car Parts in the Automotive Industry
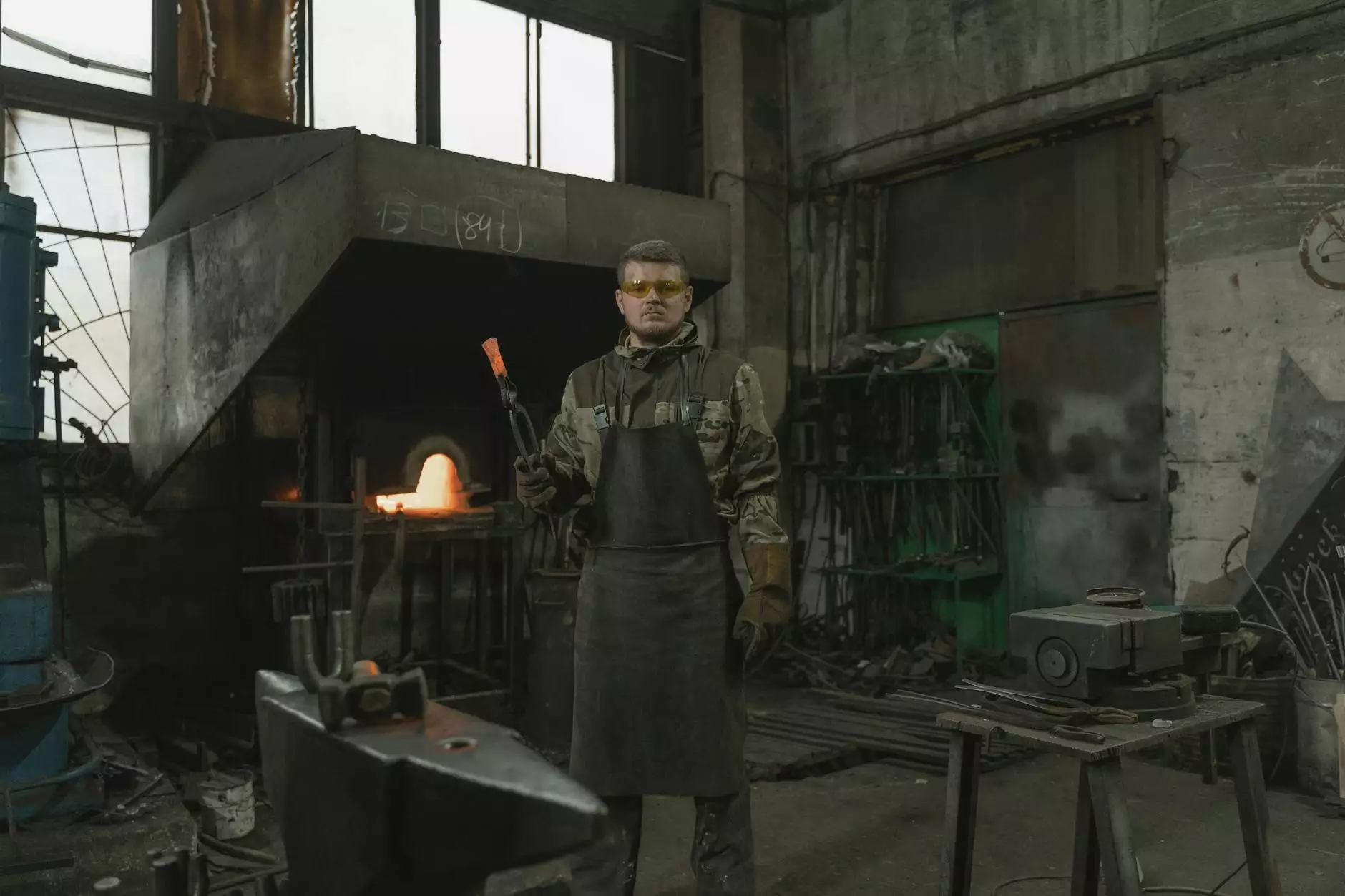
Forged carbon car parts have emerged as a revolutionary choice in the automotive sector, continually challenging traditional materials such as aluminum and steel. The adoption of forged carbon, a composite material known for its superior properties, is reshaping the way car manufacturers design and produce vehicles. This article delves into the myriad advantages of forged carbon car parts, exploring their applications, benefits, and the future they signify for automotive innovation.
What is Forged Carbon?
Forged carbon is a type of composite material that combines short carbon fibers with a resin matrix. The manufacturing process involves compressing these carbon fibers under high pressure and temperature to create a lightweight, strong, and durable product. Unlike traditional carbon fiber, which uses long continuous strands, forged carbon utilizes shorter fibers that are randomly oriented, resulting in unique mechanical properties.
Benefits of Forged Carbon Car Parts
The growing popularity of forged carbon car parts in the automotive industry can be attributed to several key benefits:
- Lightweight: One of the most significant advantages of forged carbon is its exceptional strength-to-weight ratio. By replacing heavier materials, such as steel, automakers can produce lighter vehicles that improve fuel efficiency and enhance performance.
- Durability: Forged carbon is renowned for its remarkable toughness and resistance to impact, making it an ideal choice for components that require high strength under stress.
- Aesthetics: The unique appearance of forged carbon offers a modern and stylish look, appealing to automotive enthusiasts who seek customization options for their vehicles.
- Corrosion Resistance: Unlike metal parts that can corrode over time, forged carbon does not rust, making it a long-lasting choice for automotive applications.
- Versatility: This material can be molded into various shapes and sizes, allowing for a wide range of applications in vehicle design.
Applications of Forged Carbon in Automotive Manufacturing
Forged carbon is making its mark in numerous segments of the automotive industry. Here are some applications where it is increasingly utilized:
1. Body Components
Many manufacturers are turning to forged carbon for body panels and exterior components. Its lightweight nature facilitates better performance and efficiency.
2. Interior Parts
Forged carbon can be found in high-end vehicle interiors, enhancing aesthetic appeal with its unique patterns and textures while providing the durability required for frequent use.
3. Performance Components
In racing and performance vehicles, forged carbon parts are used for components such as spoilers, hoods, and chassis elements, contributing to lower weight and improved aerodynamics.
4. Custom Accessories
Car enthusiasts and tuners are increasingly incorporating forged carbon into custom modifications, offering an aesthetic edge and performance benefits simultaneously.
Comparing Forged Carbon to Other Materials
To appreciate the benefits of forged carbon car parts, it is essential to compare them to other commonly used materials in the automotive sector:
MaterialWeightDurabilityAesthetic AppealCostForged CarbonVery LightweightHighModern LookModerate-HighAluminumLightweightModerateStandard LookLow-ModerateSteelHeavyHighStandard LookLowCarbon FiberLightweightHighSleek LookHighThe Market for Forged Carbon Car Parts
The market for forged carbon car parts is expanding rapidly, driven by increasing interest in lightweight materials offering enhanced performance. As awareness grows about climate change and sustainability, manufacturers are being pushed to seek solutions that improve fuel efficiency and reduce emissions. The transition to electric vehicles also emphasizes the need for lighter components, positioning forged carbon as a prime candidate for future developments in the automotive industry.
Challenges and Considerations
While the advantages of forged carbon car parts are promising, there are still challenges in their widespread adoption:
- Cost: Forged carbon can be more expensive than traditional materials, which may deter some manufacturers, especially in the mass production of vehicles.
- Manufacturing Techniques: The technology and processes involved in producing forged carbon parts are advanced and require investment in specialized machinery.
- Education: There is a need for greater education within the automotive industry regarding the benefits and applications of forged carbon to encourage more manufacturers to make the switch.
The Future of Forged Carbon in Automotive Design
As innovations continue to emerge, the future of forged carbon car parts looks bright. Major automotive brands are investing in research and development to explore new applications and production methods. Key trends include:
1. Integration with Advanced Technologies
The rise of automation and smart manufacturing practices can enhance the efficiency of producing forged carbon parts, reducing costs and improving quality.
2. Sustainability Initiatives
With a global focus on sustainability, forged carbon’s recyclability and lightweight properties contribute to lower emissions, aligning with environmentally friendly practices.
3. Customization Trends
As car personalization becomes more popular, the unique look of forged carbon allows manufacturers to offer consumers exciting customization options.
Conclusion
Forged carbon car parts represent the forefront of innovation in the automotive industry, combining durability, lightweight design, and aesthetic appeal. As more manufacturers recognize the advantages of this revolutionary material, forged carbon is set to become a staple in vehicle design and production. At customclass.net, we are committed to showcasing the best in auto parts & supplies, embracing today's advancements like forged carbon to enhance performance and style for automotive enthusiasts worldwide.