Understanding Plastic Mold Manufacturing: A Comprehensive Guide
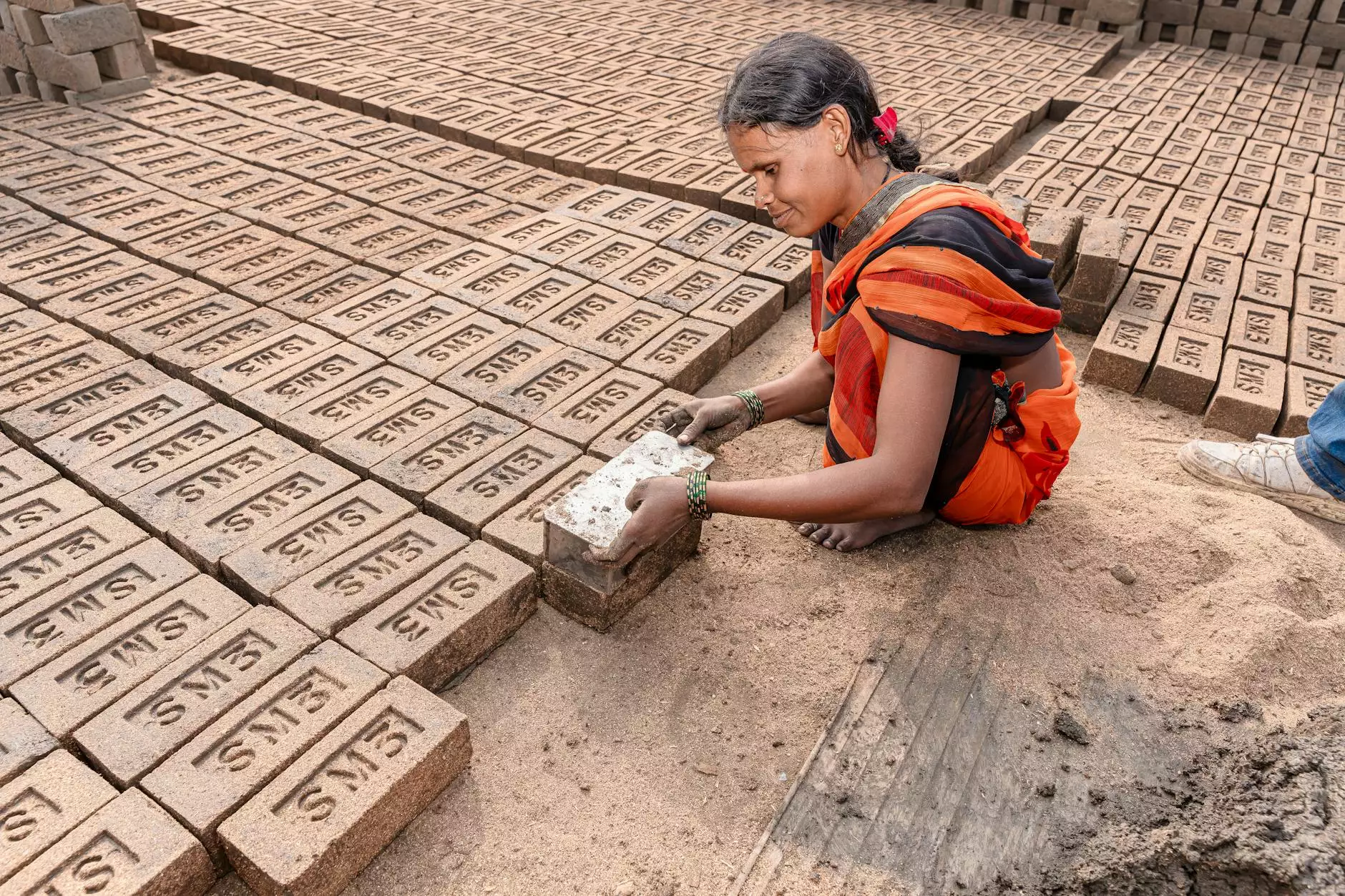
In the ever-evolving landscape of manufacturing, the role of a plastic mold manufacturer is paramount. As businesses strive for efficiency and innovation, they increasingly turn to plastic mold manufacturing due to its versatility, cost-effectiveness, and the ability to produce complex designs with excellent precision. This article delves into the intricacies of plastic mold manufacturing, highlighting its processes, applications, advantages, and the significant impact it has across various industries.
The Importance of Plastic Mold Manufacturing
Plastic mold manufacturing is crucial in creating a vast array of products that we encounter in our daily lives. From automotive components to consumer goods, the capability to produce high-quality plastic parts at scale is indispensable. The manufacturing process not only allows for the rapid production of items but also ensures that they meet the necessary specifications and standards required in different industries.
What is Plastic Mold Manufacturing?
Plastic mold manufacturing refers to the process of creating a mold used to shape plastic materials into specific forms. This involves several stages, including:
- Design and Prototyping: Initial designs are created, often using CAD (Computer-Aided Design) software, to visualize the end product.
- Mold Creation: Using high-quality steel or aluminum, manufacturers create the molds based on the specifications derived from the design.
- Injection Molding: Plastic materials are injected into the molds, where they cool and solidify into the desired shape.
- Finishing: Post-production processes like trimming, polishing, and painting are conducted to ensure the product is market-ready.
The Process of Plastic Mold Manufacturing
The manufacturing process can be broken down into the following detailed steps:
1. Design and Engineering
The foundation of any successful plastic mold product is a robust design. Engineers collaborate with designers to create a detailed blueprint that specifies dimensions, tolerances, and functionalities. Tools like 3D modeling and simulation software are used to predict how the molded part will behave under various conditions.
2. Mold Fabrication
This stage involves the actual creation of the mold. It is typically made from two main types of materials:
- Steel: Known for its durability and ability to withstand repeated use, it is ideal for high-production runs.
- Aluminum: A lighter option that allows for faster machining and is suitable for lower-volume productions.
Using CNC (Computer Numerical Control) machining, the mold components are precisely crafted to ensure high fidelity to the original design.
3. Injection Molding
Once the mold is complete, the injection molding machine comes into play. Plastic pellets are heated until they become molten and then injected into the mold under high pressure. This process allows for the creation of complex shapes and features that would be challenging to achieve with other manufacturing methods. After cooling, the mold is opened, and the newly formed part is ejected.
4. Quality Control
Following production, rigorous quality control measures are implemented. This includes dimensional checks, visual inspections, and functional tests to ensure that each part meets the required standards. Any discrepancies are addressed immediately, ensuring that only high-quality products reach the market.
Applications of Plastic Mold Manufacturing
The versatility of plastic mold manufacturing allows it to serve various industries, including:
- Automotive: Components such as dashboards, panels, and exterior trims.
- Consumer Goods: Everyday items like containers, toys, and household appliances.
- Medical: Devices and components that require stringent quality standards, such as syringes and packaging.
- Aerospace: Lightweight parts that contribute to fuel efficiency and performance.
- Electronics: Housings for gadgets and equipment, ensuring protection and aesthetic appeal.
Advantages of Using Plastic Molds
The use of plastic molds offers numerous advantages to manufacturers and businesses:
1. Cost-Effectiveness
Once the initial investment in mold creation is made, the cost per unit decreases significantly with high-volume production, making it an economical choice for large batches.
2. Precision and Repeatability
Plastic molds provide exceptional precision, ensuring that each product produced is consistent with the one before it. This repeatability is vital for maintaining quality standards.
3. Complex Geometries
Plastic molding can achieve intricate designs that may be impossible with traditional manufacturing methods. This capability enables products to be both functional and visually appealing.
4. Short Lead Times
The efficiency of the injection molding process allows for shorter lead times compared to other manufacturing methods. This agility can be crucial in fast-paced industries.
5. Versatile Material Options
A wide range of plastic materials can be used in the molding process, each offering different characteristics like strength, flexibility, and temperature resistance. This versatility enables manufacturers to choose the optimal material for their product's specific needs.