The Future of Manufacturing: Exploring Rapid Prototype Injection Moulding
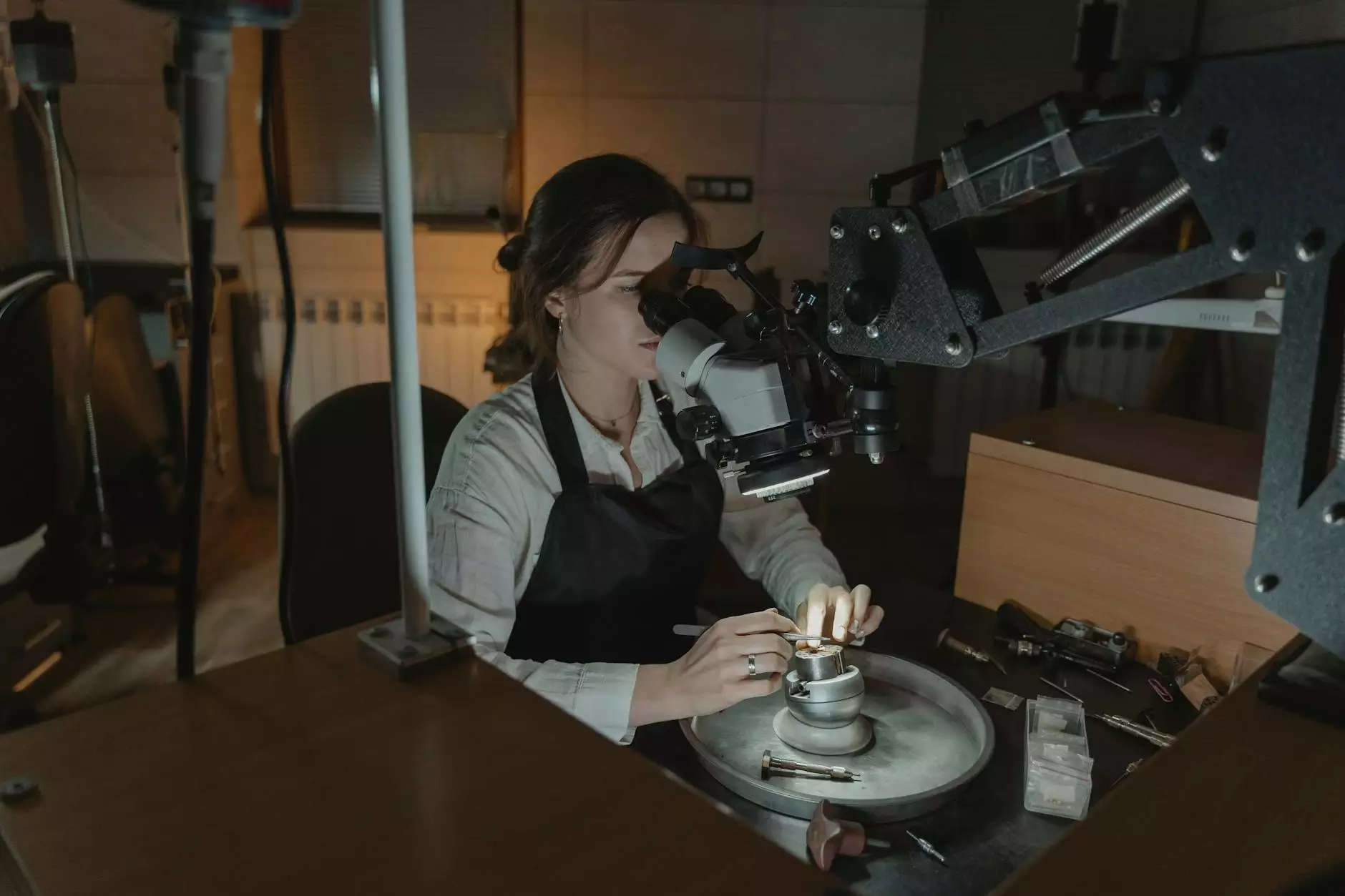
In recent years, the manufacturing industry has witnessed a significant evolution, thanks to transformative technologies like rapid prototype injection moulding. As companies continuously seek to enhance their production processes, the demand for efficient, cost-effective, and precise manufacturing techniques becomes paramount. This article delves deep into the intricacies of rapid prototype injection moulding, its advantages, applications, and its role in metal fabrication, particularly for businesses like DeepMould.net.
What is Rapid Prototype Injection Moulding?
Rapid prototype injection moulding is a manufacturing process that uses advanced methods to create prototype models efficiently and precisely. It involves the following steps:
- Design Creation: Utilizing CAD (Computer-Aided Design) software, designers create detailed 3D models of the desired product.
- Material Selection: Appropriate materials are chosen, considering the end-use and performance expectations.
- Mould Fabrication: A mould is created using techniques such as 3D printing or CNC machining, allowing for quicker turnaround times.
- Injection Moulding: The molten plastic or metal is injected into the mould, where it cools and solidifies into the desired shape.
- Quality Testing: Finished prototypes undergo rigorous testing to ensure they meet design specifications and functionality.
The Benefits of Rapid Prototype Injection Moulding
Implementing rapid prototype injection moulding offers several advantages for businesses, particularly those involved in metal fabrication:
- Accelerated Time-to-Market: The speed of production allows companies to reduce the time needed to bring a product from concept to market. This rapid pace can significantly improve a company's competitive edge.
- Cost-Effective Prototyping: Traditional prototyping can be expensive and labor-intensive. Rapid prototype injection moulding reduces costs through less material waste and quicker turnaround times.
- Design Flexibility: With advanced design capabilities, alterations to prototypes can be made swiftly, allowing for real-time adjustments based on feedback and testing insights.
- High Precision and Quality: The method ensures a high degree of accuracy in the final product, optimizing performance and quality that meet industry standards.
- Material Versatility: This process supports various materials, from plastics to metals, offering immense flexibility depending on the project's requirements.
Applications of Rapid Prototype Injection Moulding in Metal Fabrication
The versatility of rapid prototype injection moulding makes it applicable across numerous industries in metal fabrication, enhancing the functionality and innovation of products. Here are notable applications:
1. Automotive Industry
In the automotive sector, rapid prototype injection moulding plays a critical role in developing components such as dashboard panels, gears, and various connectors. By creating prototypes quickly, manufacturers can test design iterations more effectively, significantly enhancing the end product's safety and performance.
2. Aerospace Sector
The aerospace industry demands precision and reliability, making rapid prototype injection moulding exceptionally valuable. Manufacturers can produce lightweight and robust parts that meet stringent regulations while reducing lead times.
3. Consumer Electronics
With the constant evolution of technology, rapid prototyping allows manufacturers to produce intricate parts for smartphones, tablets, and wearable devices. Enhancements in design and functionality can be tested quickly, providing consumers with cutting-edge products on a timely basis.
4. Medical Devices
The medical industry benefits greatly from rapid prototype injection moulding. The ability to create precision instruments and components on a rapid basis enhances product development cycles while adhering to rigorous safety standards. Devices such as surgical instruments, dental products, and diagnostic equipment are now developed using this method.
Challenges and Considerations
While rapid prototype injection moulding offers numerous advantages, there are challenges to consider. Businesses must be aware of the following:
- Initial Setup Costs: Although cost-effective in the long run, initial investments in equipment and tooling can be significant.
- Material Limitations: Not all materials are suitable for rapid injection moulding processes. Companies must ensure compatibility with their designs.
- Subtle Design Changes: Minor alterations in the design can sometimes lead to significant adjustments in the mould, impacting time and cost.
Future Trends in Rapid Prototype Injection Moulding
The future of manufacturing is bright for rapid prototype injection moulding. As technology advances, several trends are shaping its landscape:
1. Enhanced Automation
Automation in the moulding process is likely to improve efficiency and reduce human error. Factories will see the integration of AI and machine learning, leading to smarter production lines.
2. Advanced Materials
The development of new materials will expand the capabilities of rapid prototype injection moulding. This includes bio-based plastics and advanced metals that can withstand extreme conditions.
3. Sustainability Practices
As industries focus on reducing their environmental footprint, rapid prototype injection moulding will evolve to include more sustainable practices, including material recycling and reduced energy consumption during production.
4. Increased Customization
With the rise of consumer demands for personalized products, manufacturers will leverage rapid prototype injection moulding to enhance customization capabilities, offering tailored solutions to their clientele.
Choosing the Right Partner for Rapid Prototype Injection Moulding
Partnering with the right manufacturing firm is essential to utilizing rapid prototype injection moulding effectively. Businesses should consider the following criteria when selecting a partner:
- Experience and Expertise: Ensure the company has a proven track record in rapid prototype injection moulding.
- Quality Standards: Look for certifications and adherence to industry quality standards that ensure high-quality production.
- Customer Support: Evaluate the level of support and collaboration offered throughout the prototyping and production process.
- Technological Capabilities: Ensure the company utilizes the latest technologies and materials to deliver innovative solutions.
Conclusion
Rapid prototype injection moulding is not just a trend; it's the future of manufacturing, particularly in the metal fabrication sector. This revolutionary process streamlines production, enhances design capabilities, and allows companies to bring innovative products to market faster and more efficiently. Businesses like DeepMould.net are at the forefront of this innovation, providing cutting-edge solutions that cater to various industry needs.
As you consider your next project, think about the potential of rapid prototype injection moulding to elevate your manufacturing processes, drive efficiency, and ultimately enhance your competitiveness in the market. The future is here, and it’s shaping the way products are designed and produced.